-
-
EPOXY COATING FOR STEEL PIPE & METAL EQUIPMENT
$155.00 - $195.00 -
Industrial Grade Textured Non Slip Epoxy Coating
$130.00 - $165.00 -
Epoxy Coatings For Marine Applications
Marine Epoxy Coating Applications
ArmorGarage manufactures several products for ship interiors and marine-based infrastructure applications. From heavy-duty non-slip textured coatings to direct-to-metal epoxy paint for piping, tanks, structural members, pumps, outdoor ductwork, metal building exteriors, and machinery found in large processing plants.
Each product is highly resistant to chemical and saltwater exposure, engineered to withstand high impacts and abrasion in harsh environments, outlasting other coatings you may have used in the past. Our coatings can go over most other coatings and rusted steel with minimal prep to get down to a tight rusted surface, reducing costly downtime, material, and labor costs. See our full line of products below. Contact us with any questions. We have a lot of different products, and our experts can guide you to the right one and answer any application questions. Fill out a Quote Request for prompt project pricing and volume discounts.
On Ship - Onshore - Offshore Epoxy Coatings
Just about every square foot of ships and marine-exposed infrastructure needs to be coated. We make an epoxy coating for all of it: floors, pipes, pumps, walls, structural members, and machinery. If it needs protection from corrosion and wear, we’ve got it covered.
Our Marine590 Epoxy Coating is amazing, it covers every type of steel surface inside or out with a thick, durable finish that anyone who can work a roller can apply. This coating can be applied to wet surfaces, tight rust, and even underwater! This coating does it all. It can even be used to repair leaking underwater steel or concrete when mixed with SilicaFlour/Sand to form a grout-type consistency. All our coatings are easily applied by in-house maintenance or painting staff. Available in Light Gray, Medium Gray, and White. Custom colors, including all safety colors, are available on bulk orders of 40 gallons or more.Contact us with any questions and pricing via sales@armorgarage.com or Request A Quote.
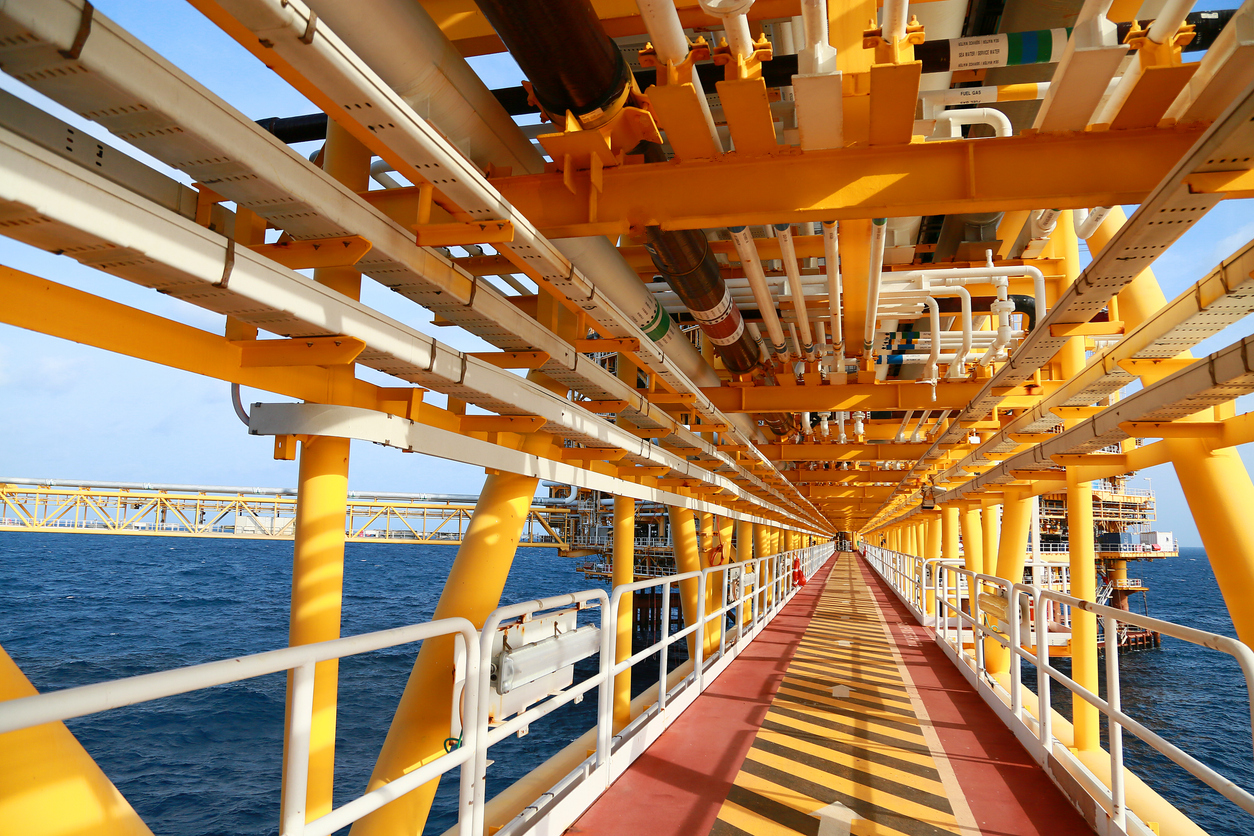
Epoxy Solution For Rusty Steel
This was an outdoor industrial plant that was in lack of upkeep until the plant owners decided it was time to do something. This image is of the steel surfaces sandblasted to remove all loose rust and paint. Then it was sprayed with two coats of our Outdoor Steel Epoxy. As you'll see on the next slide, the transformation was pretty amazing. Contact us with any questions about the product or its application and for prompt project pricing via sales@armorgarage.com or Request A Quote.
Outdoor Steel Epoxy Coating
The ArmorGarage Outdoor Steel Epoxy Coating is a single-component, easy-to-use coating that is both economical and a high-performance coating. It has some amazing characteristics, can be rolled, brushed, or sprayed onto any steel surface with tight rust or previous coating. Dries fast in 1-2 hours for a fast second coat if needed. Can handle operating temperatures up to 400 degrees, making it suitable for hot exhausts. Can be applied in cold weather down to 20 degrees and is extremely saltwater corrosion resistant and chemical resistant. At a coverage rate of 300-325 sf/gal, it makes it an economical solution to your steel infrastructure issues. Covers in one coat in most cases.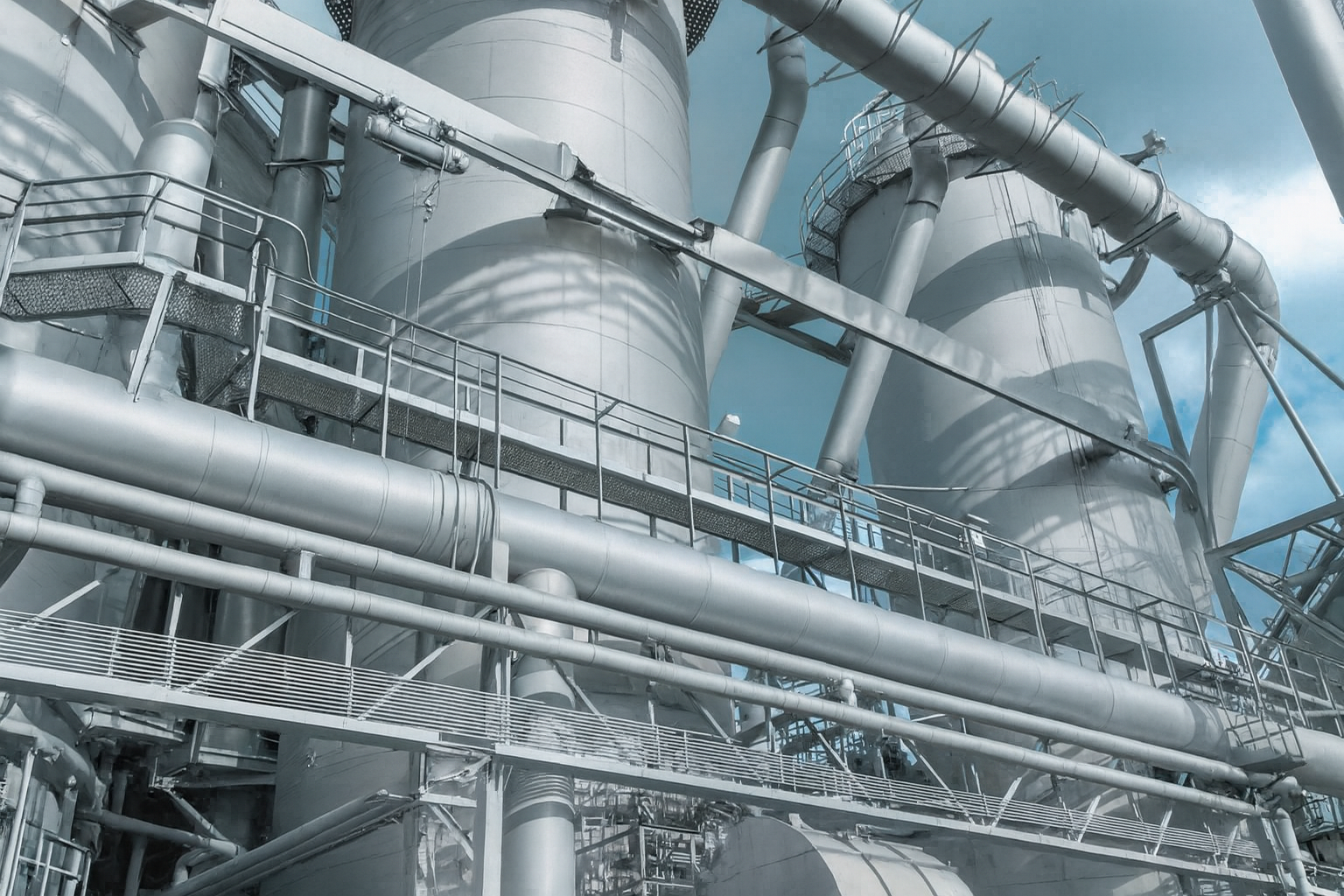
Product Features
Extra Thick Formulations
Easy To Order & Apply
Made To Last
Great Customer Service